Biomethanation Shows Potential For Waste To Energy Projects In India
Salem in Tamilnadu, accounts for almost 70% of sago (or cassava) production in India. Many industries such as sago, tannery, rubber, etc. release toxic effluents, contaminating the environment.
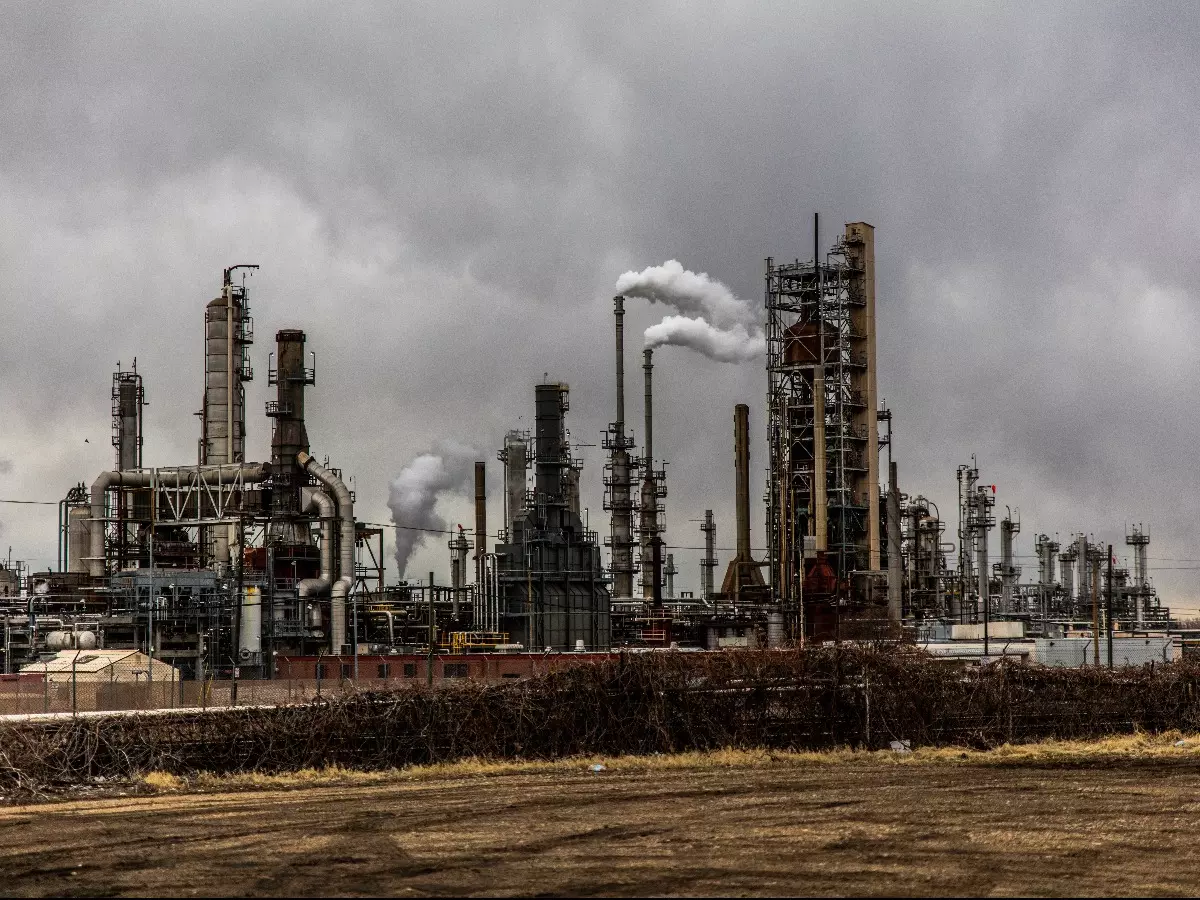
Salem in Tamilnadu, accounts for almost 70% of sago (or cassava) production in India. Many industries such as sago, tannery, rubber, etc. release toxic effluents, contaminating the environment.
¡°The government has installed many common effluent treatment plants, but they are idle because they guzzle a lot of power. The industries are not able to spend that kind of money to treat waste,¡± says S. Kamaraj, former scientist at Tamilnadu Agricultural University (TNAU), who runs the NGO Non-Conventional Energy and Rural Development.
Polluting industries
Without treatment of this waste, effluents, particularly from the sago, rubber or tannery industries are let into the environment, and it ruins the soil and water. ¡°Even the water may not fit for consumption, and if this is used to irrigate, it will kill the plants, or they will not grow at all¡±, says Kamaraj.
Unsplash/representational image
Also, releasing the untreated toxic waste into the environment is a violation of norms from the Tamilnadu Pollution Control Board (TNPCB). Kamaraj explains, ¡°If the chemical action demand (COD) level in the wastewater is more than 250 mg per litre, it is not supposed to led into the canal, river or pond.¡±
However, since mostly these are opened out in the night or during rainy season, there is less action that could be taken by the TNPCB. ¡°When they come across such cases, penalties are there, or they face closure threats, but it is not effectively implemented perhaps, due to livelihood,¡± says Kamaraj.
Waste to energy
High costs of installing effluent treatment plants, and then spending for hefty power bills is beyond the capacity of industries. ¡°If a small industry is earning Rs. 2-3 lakh per month, they end up paying electricity bills of a lakh a month. And for installing a system of aerobic treatment, Rs. 4-5 lakhs have to be spent for operating the system. The industry will not be able to do it; it is loss for them,¡± says Kamaraj.
And for these very reasons, Kamaraj believes biomethanation is a solution. He says, ¡°My research focused on how instead of consuming power, we can generate power during the treatment itself through anaerobic digestion.¡±
Biomethanation is a European technology where the industrial waste can be treated without impacting the environment. Also biogas from such industries could be used as an alternative source of energy within the factory, saving huge electricity bills. Kamaraj has been consulting many industries on efficient use of biomethanation to treat waste and also produce energy from this waste. The water from this treatment can be used for agriculture as well.
Unsplash/representational image
¡°With biomethanation, instead of consuming Rs 5 lakhs for power, industries will be able to make Rs 2-3 lakh per month as additional income. But this technology has not reached the people¡±, says Kamaraj.
Larger industries who have installed this in the sago industry have benefited. ¡°Earlier, diesel was required in addition to biogas, but nowadays 100% biogas plants are available. Not a drop of diesel is needed. One can feed the biogas continuously run without any conventional fuel of diesel, petrol; that technology is available now. Companies like Cummins, Kirloskar, they are developing 100% biogas engine also,¡± he says.
In sago industry, boilers are used. Kamaraj says, ¡°Boiler fuels are expensive. Here, they can replace it with biogas. Similarly, instead of going for conventional energy, they could cater to their energy demand by shifting to biogas.¡±
Today, sago industries which have installed biomethanation have switched over to 100% biogas-run engine. Kamaraj says, ¡°For roasting the sago, they use the dryer. It is costly, also, the uniformity was also not there due to humidity, rainfall or sunlight. Further, with open drying, bird droppings would fall. By maintaining biogas, they are now roasting sago through this and there are good benefits.¡±
Installation costs
The cost of setting up biomethanation plant starts from Rs. one lakh to Rs. 10 crore depending on the capacity. Kamaraj says, ¡°The MNRE is giving a subsidy of Rs. 1-4 crores for the project cost that goes up to Rs. 10 crores. However, the payback period is less than two to three years.¡±
Initially, there were investment hesitancies. Also Kamaraj believes smaller industries and medium industries would not be able to spend much of this technology. He says, ¡°The bank is not coming forward to provide the required loan. If this technology benefits the government and the industry then, it should be encouraged. It will be motivating for the PCB to adopt this technology, then we can rope in the industries.¡±
Unsplash/representational image
Sago industry has their own association called Sago Serve. Associations like these help industries come forth to adopt such a technology.
¡°It is the right time that policymakers should join end users, industries, NGOs, then this could be beneficial to them,¡± says Kamaraj.
The writer is a Coimbatore based freelance contributor and a winner of Asian Environmental Journalism Award 2019; Environmental Journalist of the Year, Environmental Story of the Year I Prem Bhatia Award for Excellence in Environmental Reporting 2019 I Statesman award for environmental reporting 2015 I Earth Journalism Network grantee I Fellow: UN Water, IUCN, Asia Europe Foundation. DW Climate Change Reporting Fellow South Asia.