Researchers Build World's 1st Plastic Made From Plant Oil, Not Fossil Fuels
The plastics are developed from newer materials -- plant oils -- that make it a low-waste, environmentally friendly alternative for the otherwise fossil-fuel based plastics.
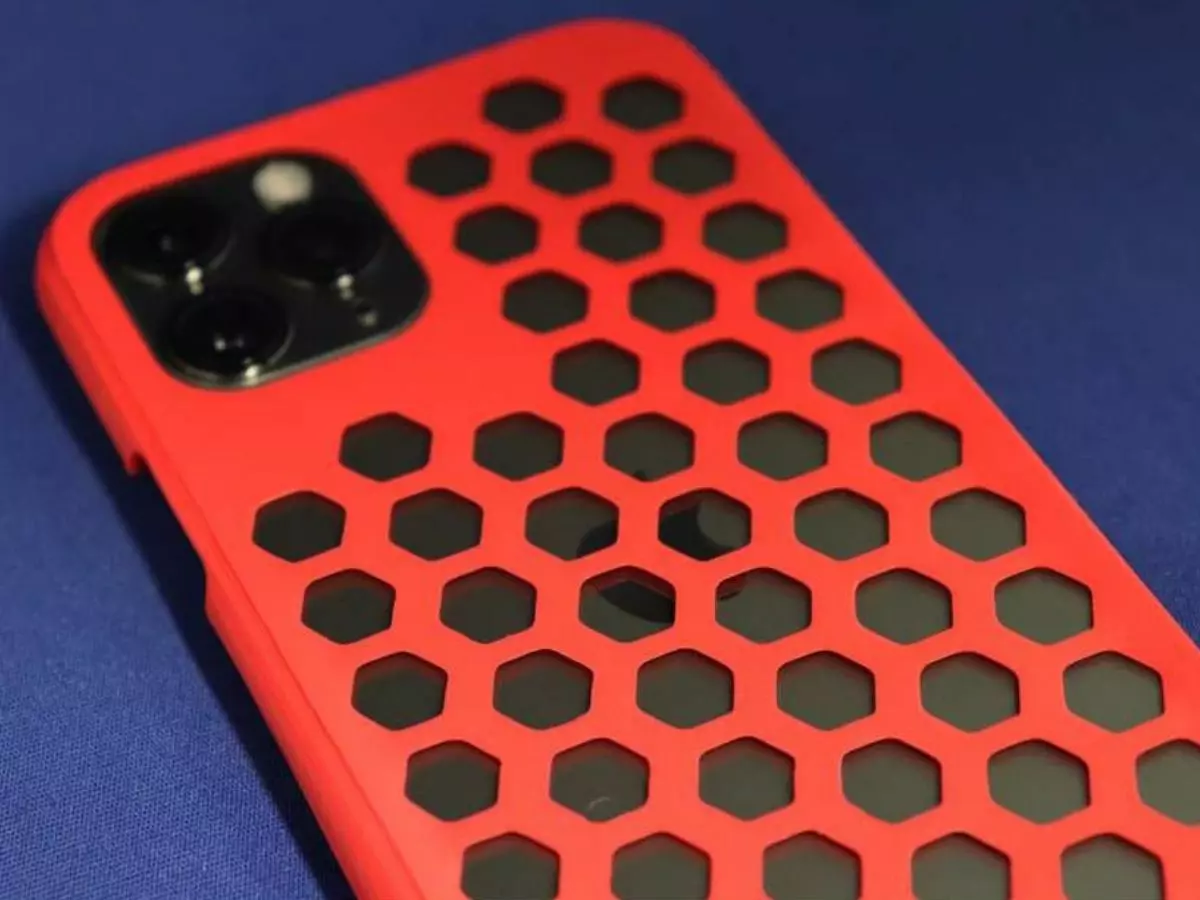
German researchers have developed two sustainable plastic alternatives to high-density polyethene that are capable of being chemically recycled and reused for nearly 10 times efficiently.
Stefan Mecking
Also Read: Researchers Create Plastic That 100% Breaks Down In Sunlight Within A Week
Developed by researcher Stefan Mecking, department chair of chemical materials science at the University of Konstanz in Germany (study published in Nature) the new plastic has breakaway points engineered on a molecular level to allow for easy processing.
Developed using plant oils
The plastics are also developed from newer materials -- plant oils -- that make it a low-waste, environmentally friendly alternative for the otherwise fossil-fuel based plastics.
Today, plastic recycling is done mechanically -- plastic pieces are segregated, sliced and then made into tiny pellets which are then reused for creating new plastic objects. However, researchers are trying to bring in a different method of recycling -- chemical recycling -- that breaks down long chains of plastic polymers with hearts or solvents to get to the material¡¯s initial monomer components.
But chemical recycling comes with its challenges, mainly due to plastic¡¯s strong carbon to carbon bonds in its molecular structure. To break these bonds it requires a ton of heat. For instance, polyethene takes 600 degrees celsius of heat to break those bonds to get access to the monomers which is later chemically recycled at a rate lower than 10 percent.
Bonds that break easily
However, the novel plastic developed by researchers from the University of Konstanz had chemical bonds that easily break far more easily -- researchers used two different materials which were forms of polyester and polycarbonate which were then placed in ethanol or methanol with a catalyst at 120 degrees Celsius or 150 degrees celsius without a catalyst.
The recrystallized plastic is then cooled and filtered out. They were able to recover 96 percent of the initial material in the case of polycarbonate.
Also Read: 10 Innovative Tech Solutions To Help Curb Plastic Pollution
Moreover, researchers found that the recycling process worked even with the presence of plastic dye or fillers. In fact, the plastics also recovered successfully when other kinds of plastic were included in the solvent.
The reason plant oils were chosen as the material to synthesize the plastics were due to their useful long chains. Moreover, they¡¯re more sustainably sourced than crude oil or other fossil fuels.
Stefan Mecking
Also Read: Japan Plastic Waste: Government Orders 100% Plastic Recycle, Reuse & Collection
Recycled plastics are still as efficient
The new plastics also had a density similar to that of polyethene. The plastic was also found to possess comparable properties like structure, molecular weights and elasticity, although polycarbonate and polyester had lower melting and crystallization points. Moreover, these plastics could degrade faster too due to its engineered breakpoints.
One place where this method isn¡¯t as feasible is pricing. Ethylene is the cheapest option for the chemical industry, so convincing brands to make the switch to a more expensive alternative could be more challenging, say researchers.